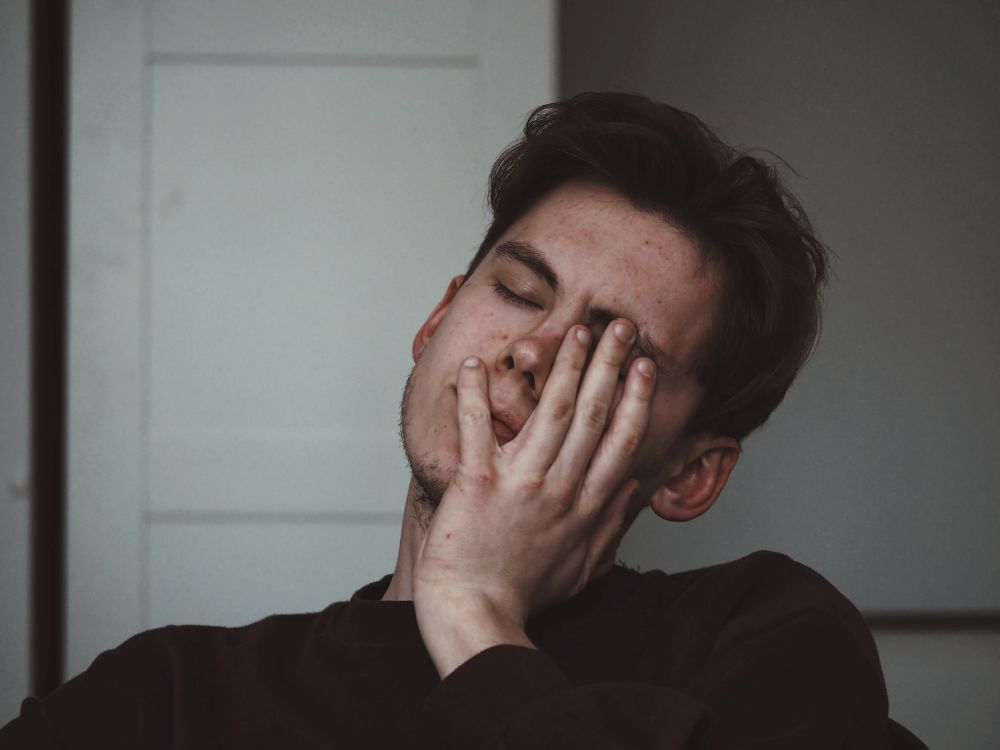
You’ve told them umpteen times. You’ve documented everything clearly. You’ve held safety days, you run toolbox talks… perhaps you’ve even implemented a fully blown behavioural safety programme.
So why are people not following the oh-so-clear procedures??!!
A just culture recognises 9 different causes of human failure. In our experience, it’s only around 5% of incidents that can be described as individual violations – that is, a deliberate, self-serving decision not to follow procedures. This begs the question, what’s happening in the other 95% of cases? Let’s take a deeper dive.
What kind of “failure to follow procedure”?
Tom has been working on site for over ten years and his knowledge and experience are appreciated in the company. Yet there are still occasions when he has to be hauled up for not following procedure properly.
To get to the bottom of this, we have to understand the types of mistakes that Tom is making – and indeed, whether it really is Tom that’s making mistakes. These could include:
Beware of making assumptions about which and how many of the above apply! An effective resolution will only be achieved through having a clear understanding of the type of failure you are dealing with. Undertaking a professional safety culture survey and holding effective safety conversations with your employee(s) will help you to understand what’s in play here.
What’s behind the behaviour?
Once you’ve got an understanding of the type of procedure breach you’re looking at, you’ll have more of a clue as to where to look to address the root cause.
To give some examples:
Engagement
- Does your organisation have an aligned, well-communicated strategic narrative? Most organisations are adept at ensuring their employees know what they have to do, and how to do it. Instilling a clear conviction of why – at all levels in the organisation – is harder.
- Who were your procedures written by? Did the people that you’re expecting to use them have any input into their creation or modification?
- Do people feel empowered to talk about ways in which the procedures could be improved, simplified, or made more effective?
Communication
- Your procedures might be written in what seems plain English to you, but are they comprehendible by all employees? We’ve come across examples of procedures written in A’ level standard English when some of the people they’re written for have a reading age closer to 10. Remember people will often be too embarrassed to tell you they don’t understand.
- Are your employees clear on the why of the procedure as well as the what? Is the procedure aligned to the organisation’s strategic narrative and is it clear to people how this procedure is helping the organisation move towards its goal?
- Are effective safety conversations the norm where you work? Do people feel safe to challenge unsafe behaviours? More importantly, are safe behaviours noticed and highlighted? When was the last time you went out to catch someone doing something right?
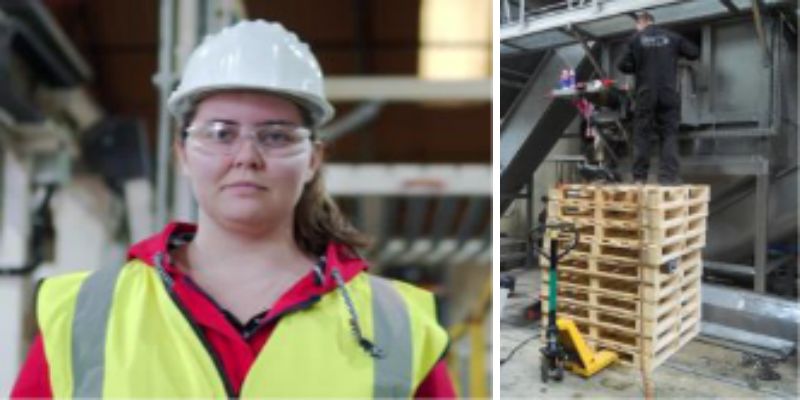
Curious to learn what makes for an effective safety conversation? Find out here.
Safety Leadership
- Are your leaders walking the walk as well as talking the talk? Or are they unwittingly or knowingly letting unsafe behaviours pass? Why might that be?
- Are employees clear on the consequences of following or not following procedures? Are these consistently followed up?
- Are leaders equipped with the knowledge and tools they need to manage their teams effectively and compassionately, fostering a culture of care?
Struggling to work out how to get your leaders to walk the walk? Take a look at our safety leadership page.
System
- Do employees have enough evidence to convince them that the procedures help them to do the job better, faster or more easily? Sometimes this has to involve making the wrong way harder as well as making the right way easier. Is the right way the easy way?
- Does the requirement to follow procedures conflict with other expectations that are given more priority within the organisation? Do production targets, operational pressures, team expectations override compliance? Does your organisation believe at its heart that (as is the case!), better safety performance leads to better overall performance?
- Physical environment – are tools, machinery, workplace layout, software, clothing/PPE designed to optimise human performance, wellbeing and overall system efficiency?
Remember – the essence of good behavioural safety is making the easy way safe.
Conclusion
When daily practice differs from documented procedure, it’s tempting to blame employee incompetence, laziness, or bad attitude.
It’s also tempting to take the ‘simple’ option and throw more training at it – whether that’s another toolbox talk or a full-blown safety day.
But if you take away nothing else from reading this post, remember cause and effect. Yes, there might be a few people in the world who come to work simply to make life difficult for their employees, but most turn up ready to do a fair day’s work for a fair day’s pay. There are always drivers for people’s behaviours – whether those behaviours are desirable or otherwise. The challenge for a safety leader is to unpick what those drivers are and work with employees to create procedures that work for everyone and a culture in which they can flourish.